Cusmat, a metaverse-based immersive skilling platform, was founded in 2018 by NIT Warangal batchmates Abhinav Ayan and Anirban Chakravorty. Its purpose is to upskill the industrial workforce in large enterprises worldwide, focusing on sectors such as mining, manufacturing, pharmaceuticals, and logistics. The goal is to increase productivity, improve safety, and reduce cycle times.
In an exclusive interview, KVS Rao, the Executive Vice President, Cusmat shares about upskilling, immersive skill modules and more.
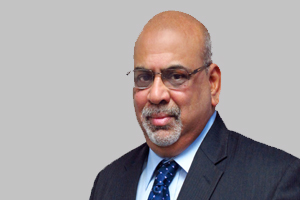
Could you provide an overview of Cusmat and its mission to upskill the industrial workforce through its metaverse-based immersive skilling platform?
According to a report by the World Economic Forum and PWC, poor skills cost the global economy $6.5 trillion, with $570 billion attributed to India alone. Cusmat’s vision is to develop the world’s largest VR upskilling infrastructure and actively contribute to the transformation of large enterprises by enhancing the skills of their workforce through immersive skilling solutions.
The company utilises digital twins and advanced technologies like AR/VR, along with proprietary physics and analytics engines. Large enterprises employ the platform for assessing, upskilling, and continuously improving the skill levels of their blue-collar workforce. The objective is to enhance operational efficiency while reducing costs, hazards, and risks.
How does Cusmat leverage augmented reality (AR) and virtual reality (VR) technologies to enhance industrial skilling? Can you explain the key features and functionalities of your platform?
With the use of AR and VR, Cusmat recreates situations and tasks performed in factories or workshops within an immersive environment. The step-by-step gamification of tasks on an AR/VR upskilling module makes learning relatable to real on-site jobs and enhances on-site performance. For blue-collar workers with hands-on skills, this medium translates into improved real-world performance and efficiency.
Cusmat’s immersive skilling platform excels in instilling the motor skills and muscle memory required by the industrial workforce. These skills cannot be easily assimilated through traditional non-interactive modes of instruction such as pen and paper or videos.
The Cusmat immersive skilling platform offers the following features and functionalities for clients:
- Upskilling with cutting-edge technology: Utilising digital twins, proprietary physics, and analytics engine, Cusmat’s Immersive Skilling platform enables upskilling of industrial workers, particularly in critical hard skill areas. This greatly improves organisational efficiency, reduces costs and risks, and can also address attrition issues.
- Focus on hard skills: Traditional classroom methods have proven inadequate for training blue-collar workers in industries like supply chain & logistics, manufacturing, and mining. Cusmat identifies the challenges faced by organisations in each of these sectors and develops simulator platforms to target these critical skills, enhancing productivity, efficiency, and safety, thereby impacting the top and bottom line of its clients.
- Immersive learning experiences: The platform creates dynamic and interactive learning experiences, allowing operators to perform tasks in a complete simulation of their job environment. This boosts engagement, knowledge retention, and skill acquisition, bridging the gap between theory and practice.
- Personalised learning paths: Cusmat’s platform offers customised learning paths based on organisational needs, skill gaps, and individual preferences. This self-paced approach ensures relevant and meaningful training, motivating employees and achieving optimal outcomes.
- Real-time performance tracking and analytics: The Cusmat Immersive Skilling platform provides robust tracking and analytics capabilities, offering insights into operator performance and progress. Real-time monitoring of completion rates, mistakes, and assessment times helps identify areas for improvement and make informed training decisions regarding future initiatives.

Cusmat has achieved significant success in a relatively short span of time. Can you share some examples or case studies that highlight the impact of your AR/VR-based industrial skilling platform on the productivity, safety, and cycle times of your customers?
Cusmat’s Immersive Skilling Platform has improved worker efficiency, increased productivity, and reduced costs. It has provided data-driven insights, reduced training time from months to days, and helped boost employee morale for enterprises. In just four years, Cusmat’s modules have trained over 60,000 individuals across 45 global enterprises in sectors such as Logistics, Mining, Manufacturing, and Pharmaceuticals.
For example, in a last-mile delivery firm, a high churn rate is common. Skill training includes handling multiple products, such as temperature control products. Since delivery personnel are the last mile connection with the customer, ensuring they have the right skills is crucial. Typically, new joiners took around 90 days to make the minimum number of error-free deliveries. With Cusmat’s Metaverse-based skilling platform, new hires could be trained and reach maximum efficiency in just 7 days, compared to the previous 90 days. This led to a 17% increase in daily deliveries.
Another case is with forklift training in a manufacturing company. The factory needed a way to evaluate operator competency before they actually operated the equipment. The goal was to effectively benchmark skill levels for each operator and understand areas of improvement. Traditional assessment methodologies did not offer individual-level data about each trainee’s learning success or struggle, which was critical for improving operator performance.
Cusmat’s immersive skilling system provided a detailed analysis of the skill sets and learning ability of the operators under training using real-time tracking and analysis. The module also ensured that 90% of the operators who underwent the immersive skilling solution cleared the required operations license test on their first attempt, compared to the previous average of 7-8 attempts.

In which sectors or industries has Cusmat primarily focused its efforts? How does your platform cater to the specific training needs and challenges faced by enterprises in sectors such as mining, manufacturing, pharmaceuticals, and logistics?
Cusmat has primarily focused on the Mining, Pharmaceuticals, Manufacturing, and Logistics sectors. Each sector presents unique requirements and challenges. Our efforts have been focused on identifying the critical skills needed in these sectors and addressing them through our Immersive Skilling platform.
Developing and implementing our immersive skilling platform for each sector requires a dedicated team of professionals and domain specialists. This multidisciplinary team includes instructional designers, software developers, 3D artists, UX/UI designers, and domain experts. Each team member brings their expertise to the project, collaborating closely to ensure the successful development and deployment of the platform.
Once a company signs up, our product team, led by a sector expert, identifies the key pain points and establishes a step-by-step process. The team then develops a skilling solution tailored to the company’s specific needs, offering a realistic and immersive training experience that enables employees to gain hands-on skills and knowledge in a safe environment.
In the manufacturing sector, challenges such as high Mean Time to Repair (MTTR), low Mean Time Between Failures (MTBF), and costly equipment maintenance have a significant impact on productivity, operational costs, and overall performance. By providing a realistic virtual environment for practicing equipment operation and troubleshooting scenarios, our platform significantly reduces training time and upskilling, leading to a noticeable decrease in MTTR. Additionally, our simulator platform minimises the need for physical equipment and associated costs.
In the Logistics sector, inefficient packaging of materials in delivery firms was a pain point that affected reputational risk and business loss. Cusmat’s team designed a detailed AR module for proper handling and packaging of materials, resulting in reduced time and error rates. Similarly, the operations of Material Handling Equipment (MHE) play a crucial role in the Logistics & Warehousing sector, directly impacting daily tonnage. We have addressed this key skill to positively impact the sector.
Upskilling the industrial workforce is crucial for enterprises seeking to improve their top-line and bottom-line performance. How does Cusmat’s immersive skilling platform contribute to achieving these outcomes? Can you provide specific metrics or success stories that demonstrate the positive impact on business results?
Our Immersive Skilling platform captures real-time data on employee performance, enabling organisations to track progress, identify areas for improvement, and make data-driven decisions. This data analytics capability helps optimise training programs and identifies patterns that impact both the top line and bottom line.
By providing realistic experiences, our skilling platform accelerates the learning curve and improves workforce proficiency. This ultimately leads to increased productivity as the workforce becomes better prepared to handle equipment and perform tasks effectively. The enhanced productivity has a positive impact on the top line by improving output and customer satisfaction.
We also continuously gather feedback from clients, trainers, and learners to refine and enhance our simulator platform. This iterative approach ensures that the platform addresses evolving industry needs, further optimising the impact on the top line and bottom line.
Here are a few measured outcomes of Cusmat training modules:
- For a delivery firm in the last-mile logistics sector: Using Cusmat’s Metaverse-based skilling platform, new hires could reach maximum efficiency in just 7 days, compared to the previous 90-day period. This led to a 17% increase in daily deliveries.
- A leading Japanese manufacturing company reduced material handling lead times by 40% and operator licensing times by 92%. Skilling improvement and monitoring also significantly reduced “Near Misses” cases, an important factor monitored by the Environmental Health and Safety team in factories.
Here are some significant metrics based on our analytics:
- 70% reduction in mean time to repair
- 20% increase in productivity
- 20% reduction in time to reach maximum efficiency
- 15% reduction in costs
What sets Cusmat apart from other skilling platforms in the market? What unique value propositions or advantages does your metaverse-based approach offer to customers?
Cusmat is the only Training and Development provider that uses AR/VR technology focused on blue-collar workers. Our modules are designed to be simple to understand and focus on building self-paced immersive skilling environments rather than relying on observation or textbook learning.
We have a proven record of reducing the time it takes for individuals to learn new skills. For example, individuals who undergo our Forklift training, which is used not only by factories but also logistics firms, are able to clear the certification in their first attempt.
Our proprietary Physics and Analytics engines make a significant difference in terms of skill retention effectiveness and measurement. We have an almost real-time feedback loop on the effectiveness of training. Many of our modules consist of two parts: the first part provides detailed instructions on the product, followed by an assessment module where individuals need to score enough points to progress to the next level.
Our most important value proposition is the substantial impact we bring to the top line and bottom line of our customers. Cusmat’s experience with industrial brands in India and some South Asian markets has shown that a workforce skilled via the Metaverse is approximately 30% more productive, 25% more efficient, and 70% safer than their peers.
Could you discuss the development and design process of Cusmat’s immersive skilling modules? How do you ensure that the training content and simulations align with industry standards and best practices?
In our journey as an immersive skilling platform, we have undertaken key initiatives that have greatly contributed to the efficiency and effectiveness of the platform we offer. These initiatives have helped us deliver impactful learning experiences and drive positive outcomes for our clients.
- Development of immersive content: We have invested significant efforts in creating high-quality immersive content, including virtual reality (VR) and augmented reality (AR) simulations that adhere to international OSHA standards. These realistic and engaging experiences enhance skill development, setting us apart from traditional training methods.
- Integration of data analytics: To measure the impact and effectiveness of our immersive skilling platform, we have incorporated a robust and proprietary analytics engine. This initiative allows us to collect and analyse data on learner performance, engagement, and progress. By tracking key metrics and generating detailed reports, we provide valuable insights to organisations, enabling them to make data-driven decisions, identify areas for improvement, and measure the return on investment (ROI) of their learning programs.
- Collaboration with industry experts: We recognise the importance of collaboration and knowledge sharing in driving excellence in the L&D field. Therefore, we have established partnerships and collaborations with industry experts, subject matter specialists, and thought leaders. This initiative allows us to tap into their expertise and insights, ensuring that our platform reflects the best practices in immersive skilling.
Given the rapid advancements in AR/VR technologies, how does Cusmat stay at the forefront of innovation and ensure that its platform evolves to meet the changing needs of industrial skilling?
Since its inception, as category creators in the Immersive Skilling space, Cusmat has remained at the forefront of industry trends, emerging technologies, and best practices. We have developed advanced analytics and reporting functionalities within our immersive skilling platform, providing detailed insights into operators’ performance. This allows organisations to track progress, identify areas for improvement, and make data-driven decisions. By embracing emerging technologies and continuously pushing the boundaries of immersive skilling, we have positioned ourselves as a leading provider in the industry, delivering transformative and impactful learning experiences. Our goal is to empower organisations to unlock the full potential of their workforce and drive positive change.

How does Cusmat address the challenges associated with deploying and scaling its platform across large enterprises globally? Are there any notable partnerships or collaborations that have facilitated your expansion and customer adoption?
We establish local sales representative partnerships in foreign countries to ensure our presence on the ground and deep understanding of local customs and nuances. This approach allows us to effectively engage with enterprises and their employees. Additionally, we are currently in discussions with global OEMs who have recognised the value of our Immersive Skilling Platform. Collaborating with them would enable us to offer our platform to their global customer base.
Looking ahead, what is Cusmat’s vision for the future of immersive skilling in the industrial sector? Are there any upcoming developments or initiatives that you would like to share with our readers?
We closely monitor not only AR/VR technologies but also all advancements that can enhance the skilling experience for enterprises. For example, we are actively exploring the application of generative AI to better interpret and predict the skill levels of operators and technicians who utilise our Skilling platform.
In addition to technological advancements, we strive to continually enhance our knowledge and understanding of various industries and sectors. This enables us to address the critical and impactful skills that can drive improvements in the top line and bottom line of our enterprise customers.
We firmly believe that scaling skilling initiatives can bring about transformative changes, not only for enterprises but also at a societal level worldwide. We take pride in playing a role in ensuring that more and more enterprises across the globe embrace and benefit from Immersive Skilling.